亚马逊斥资 4 亿美元在北安多佛开设马萨诸塞州最大的机器人仓库
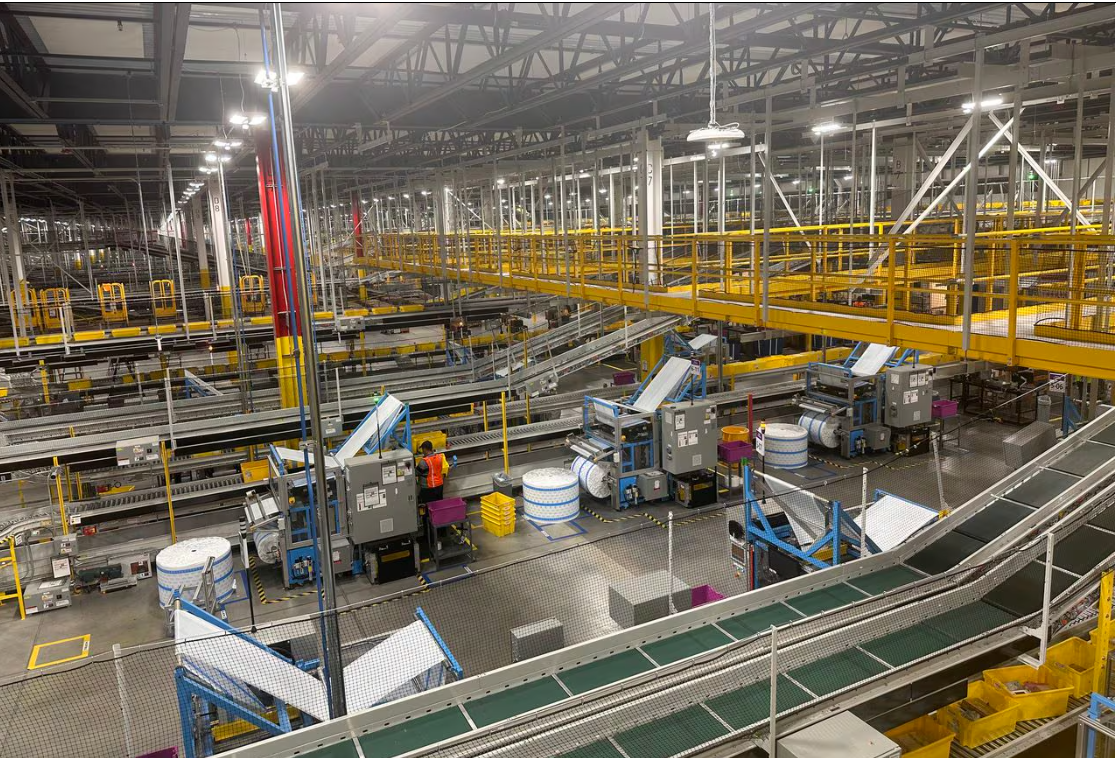
【中美创新时报2024 年 4 月 8 日编译讯】(记者温友平编译)周一(8日),亚马逊揭开了其在马萨诸塞州最大的仓库的面纱,这是一座位于北安多佛的五层仓库,面积近 400 万平方英尺,可容纳从书籍、DVD 到罐头汤等各种物品。该仓库是旧电话工厂旧址上的一处设施改建而成,将雇用 1,500 名工人,以及数千名机器人。《波士顿环球报》记者亚伦·普雷斯曼(Aaron Pressman)对此作了如下详细报道。
亚马逊表示,该配送中心位于一家前电话公司工厂的旧址上,耗资约 4 亿美元,将雇用 1,500 名员工。 该公司表示,该工厂有 66 个足球场那么大,拥有 12 英里长的传送带,每天可以处理数十万份订单。 它还拥有数千台机器人,帮助自动化货物运输。
虽然它在一月份开业,但亚马逊邀请了州长莫拉·希利(Maura Healey)以及其他州和地方官员参加周一早上的剪彩仪式。在亚马逊第二总部办公园区竞标失败后,北安多佛于 2019 年批准了该项目,并在 10 年内为该仓库提供了 2700 万美元的财产税减免。
亚马逊机器人首席技术专家泰·布雷迪在接受《波士顿环球报》采访时表示,该设施是亚马逊在马萨诸塞州的第一个高度自动化仓库。居住在马萨诸塞州的布雷迪看起来像一位自豪的爸爸,在剪彩前一天,他带领《波士顿环球报》记者参观了该设施。 “它看起来就像一个弹跳的大男孩,”布雷迪热情地说。
所有北安多弗机器人都是内部设计并在马萨诸塞州的两家亚马逊工厂之一制造的。布雷迪说,事实上,亚马逊在全球部署的 75 万个机器人全部是在马萨诸塞州制造的。(Amazon Robotics 的前身是亚马逊于 2012 年收购了位于 North Reading 的 Kiva Systems。)
“这是应用机器人技术,”他说。“他们不会在地板上做后空翻或跳舞——我喜欢这些,我明白——但他们的工作是准时、非常可靠地搬运货物。”
整个仓库的设计目的是处理单边不超过 18-1/2 英寸的物品,正好适合装入常见的黄色塑料手提袋,这是 21 世纪物流行业的血管。 新仓库的规模是亚马逊福尔河工厂处理大型货物的两倍多。
布雷迪解释说,该工厂采用了三种不同类型的机器人,旨在接管琐碎、单调和重复性的工作。
在一楼,工人们从卡车上卸下一箱箱的货物,并将所有物品装入黄色手提袋中。然后,手提箱被送到存放物品的最上面四层之一。
在每个存储楼层,都有一个巨大的中央空间被围起来,作为亚马逊 Hercules 机器人的领域——带有轮子的圆形、扁平机器,在装满存储物品的高架子下快速移动。机器人将货架盒移动到需要的地方。每个吊舱都有四个侧面的架子,每面都有 30 个或更多的小隔间,用于存放不同的物品。
在地板的边缘,高科技站的工作人员收到装满需要存储物品的手提箱。 当他们从手提袋中取出货物时,光学扫描仪会识别每件物品。 大力神机器人将一个货架吊舱带到工人工作站。 工作人员可以将物品放置在吊舱上任何看起来有足够空间的小隔间中,而激光雷达传感器则准确跟踪物品最终的位置。就像一个难以想象的复杂拼图游戏,数以百万计的物品随机分布在数千个货架上。
但系统知道每件物品在哪里。布雷迪说,当顾客在亚马逊网站上选择商品并点击订购商品进行送货时,该公司的系统会找到商品并计算出两种方式将它们运送到顾客的前门以实现冗余。
在边缘的其他站点,工作人员负责履行客户订单。空手提袋装满订单并返回一楼,在那里订单被包装和运输。
一旦准备好运输,将每个包裹运送到正确卡车的系统就依赖于另外两个亚马逊机器人。 当包裹沿着传送带流动时,一只名为 Robin 的自动化手臂会一次抬起并扫描一个包裹,然后将它们放在名为 Pegasus 的移动机器人上。然后,每个轮式 Pegasus 机器人将包裹运送到传送带上,传送带将包裹运送到正确的卡车停车位。
亚马逊表示,机器人技术的增加使用可以提高安全性并减少工人受伤。
研究工作场所自动化的波士顿大学教授戈登·伯奇表示,研究证实亚马逊的机器人减少了该公司设施中的严重伤害数量。但是,他说,他的研究还发现,重复性任务造成的不太严重的伤害有所增加。
“他们让仓库员工的工作更加安全,”伯奇说。但是,机器人中的仓库工人“不仅需要更快地工作,而且最终还会站在一个地方,一遍又一遍地执行相同的单调任务。 这种速度和重复的结合会导致工人因压力而受伤。”
北安多佛仓库的所在地几十年来一直是 AT&T 电话工厂,在 20 世纪 80 年代的鼎盛时期雇佣了多达 12,000 名工人。贝尔系统解体后,该工厂归朗讯科技所有,生产网络设备,直至 2008 年关闭。
题图:亚马逊于 2024 年 1 月在马萨诸塞州北安多佛开设了其最大的工厂,这是一个占地近 400 万平方英尺的配送中心。AARON PRESSMAN
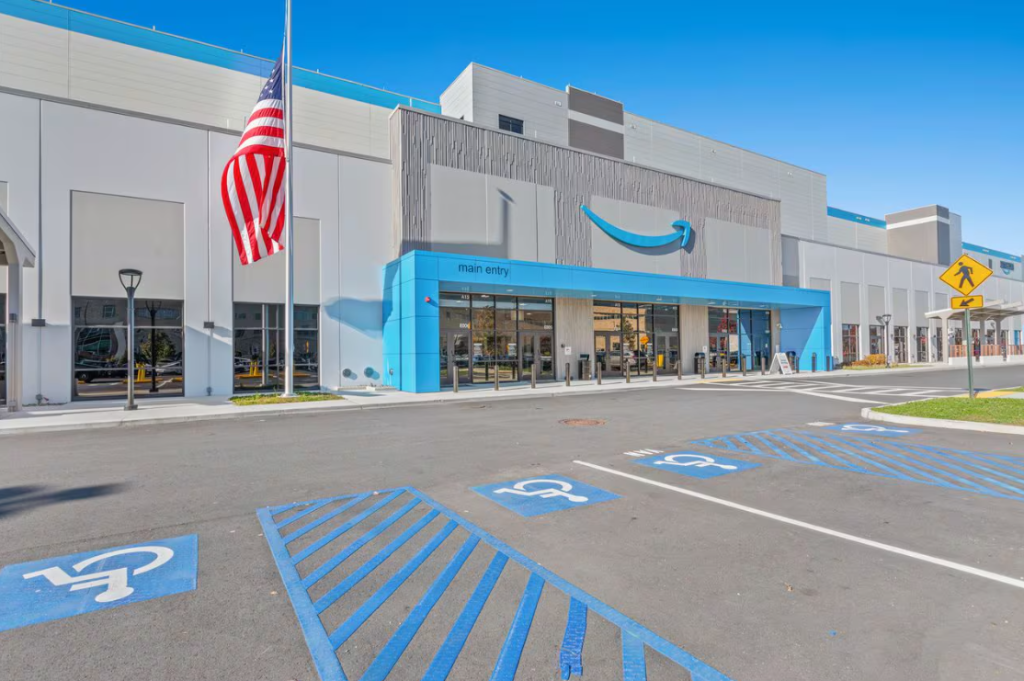
图二:周一,亚马逊揭开了其在马萨诸塞州最大的仓库的面纱,这是位于北安多佛的一座令人惊叹的五层仓库,空间近 400 万平方英尺,可容纳从书籍、DVD 到罐装汤等各种物品。ISABELA ROSA/亚马逊
附原英文报道:
Amazon debuts $400 million robotic warehouse in North Andover, biggest in the state
A facility on the site of an old telephone factory will employ 1,500 workers — and thousands more robots
By Aaron Pressman Globe Staff,Updated April 8, 2024
Amazon unveiled its largest facility in Massachusetts on Monday, a staggering five-story warehouse in North Andover with almost 4 million square feet of space to hold everything from books and DVDs to cans of soup.
The fulfillment center on the site of a former telephone company factory cost about $400 million to build and will employ 1,500 people, Amazon said. As big as 66 football fields, the facility has 12 miles of conveyor belts to handle hundreds of thousands of orders per day, the company said. It is also home to thousands of robots that help automate the movement of goods.
Though it opened in January, Amazon invited Governor Maura Healey and other state and local officials to a ribbon-cutting ceremony on Monday morning. North Andover approved the project in 2019, after losing out on a bid to host Amazon’s HQ2 office campus, granting $27 million of property tax breaks for the warehouse over 10 years.
The facility is Amazon’s first highly automated warehouse in Massachusetts, Tye Brady, chief technologist for Amazon Robotics, told the Globe in an interview. Looking like a proud papa, Brady, who is based in Massachusetts, gave a Globe reporter a tour of the facility the day before the ribbon cutting. “It just showed up like a big baby bouncing boy,” Brady said with enthusiasm.
All of the North Andover robots are designed in-house and manufactured at one of two Amazon factories in Massachusetts. In fact, all of the 750,000 robots Amazon has deployed worldwide were built in Massachusetts, Brady said. (Amazon Robotics grew out of Amazon’s acquisition of North Reading-based Kiva Systems in 2012.)
“It’s applied robotics,” he said. “They’re not doing back flips or dances out there on the floor — I love those, I get it — but they’re doing the job of moving goods on time and very reliably.”
The entire warehouse is designed to handle items that are no larger than 18-1/2 inches on a side — just right to fit in the common yellow plastic totes that are the blood vessels of the 21st-century logistics industry. The new warehouse is more than twice the size of Amazon’s Fall River facility that handles larger goods.
Brady explained that the facility employs three distinct types of robots which are intended to take over menial, monotonous, and repetitive jobs.
On the first floor, workers unload cases of goods from trucks and unpack all of the items into yellow totes. The totes are then sent to one of the top four floors where items are stored.
On each storage floor, a vast central space is fenced off as the domain of Amazon’s Hercules robots — round, flat machines on wheels that zip under tall shelving pods filled with stored items. The robots move the shelving pods where they are needed. Each pod has four sides of shelves and each side has 30 or more cubbies holding different items.
Around the edges of the floor, workers at high-tech stations receive totes filled with items needing to be stored. As they lift goods from the tote, an optical scanner identifies each item. A Hercules robot brings a shelving pod to the worker’s station. The worker can place the item in any cubby on the pod that looks like it has enough room, while a Lidar sensor tracks exactly where the item ended up. Like an unimaginably complicated jigsaw puzzle, millions of items are distributed at random across thousands of shelving pods.
But the system knows where every item is. Between the time when a customer selects items on Amazon’s website and clicks to order the items for delivery, the company’s systems locate the items and calculate two ways to deliver them to the customer’s front door for redundancy, Brady said.
At other stations around the edges, workers conduct the process of fulfilling customer orders. Empty totes are filled with orders and return to the first floor where orders are packaged and shipped.
Once ready for shipping, the system of getting each package to the correct truck relies on two other Amazon robots. As packages flow along a conveyor belt, an automated arm dubbed Robin lifts up and scans packages one at a time and sets them down on a mobile robot called Pegasus. Each wheeled Pegasus robot then carries the package to a conveyor that will bring the package to the correct truck bay.
Amazon says the increased use of robotics improves safety and cuts down on worker injuries.
Gordon Burtch, a Boston University professor who studies workplace automation, said studies have confirmed that Amazon’s robots reduce the number of severe injuries in the company’s facilities. But, he said, his research also has found an increase in less severe injuries from repetitive tasks.
“They are making the work safer for warehouse associates,” Burtch said. But, the warehouse workers among robots “are not only required to work more quickly, they also end up standing in one spot, performing the same monotonous task over and over. This combination of speed and repetition leads to more stress-based injuries among workers.”
The site of the North Andover warehouse was an AT&T telephone factory for decades, employing as many as 12,000 workers at its peak in the 1980s. After the breakup of the Bell system, the factory was owned by Lucent Technologies and made networking gear until it closed in 2008.
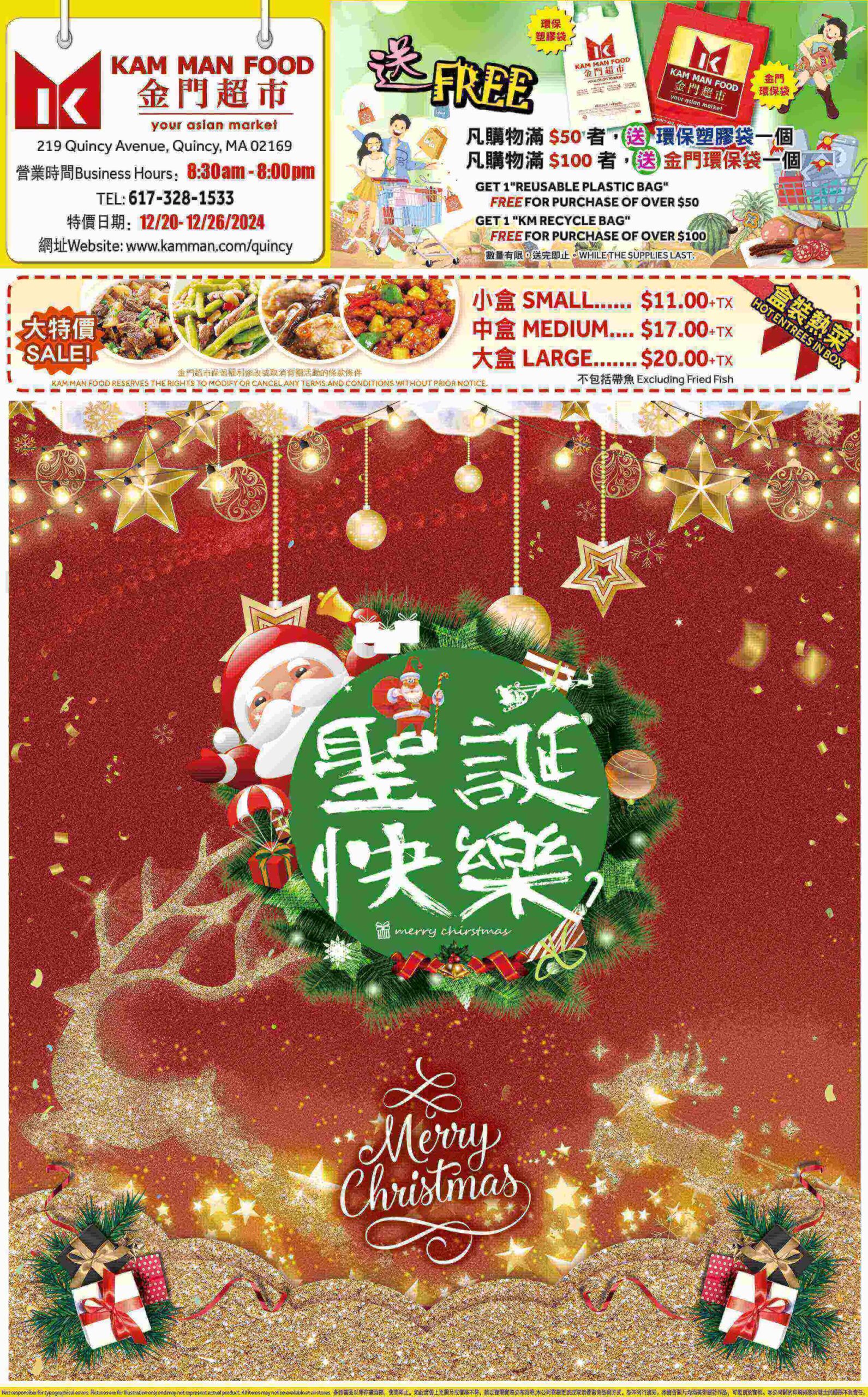